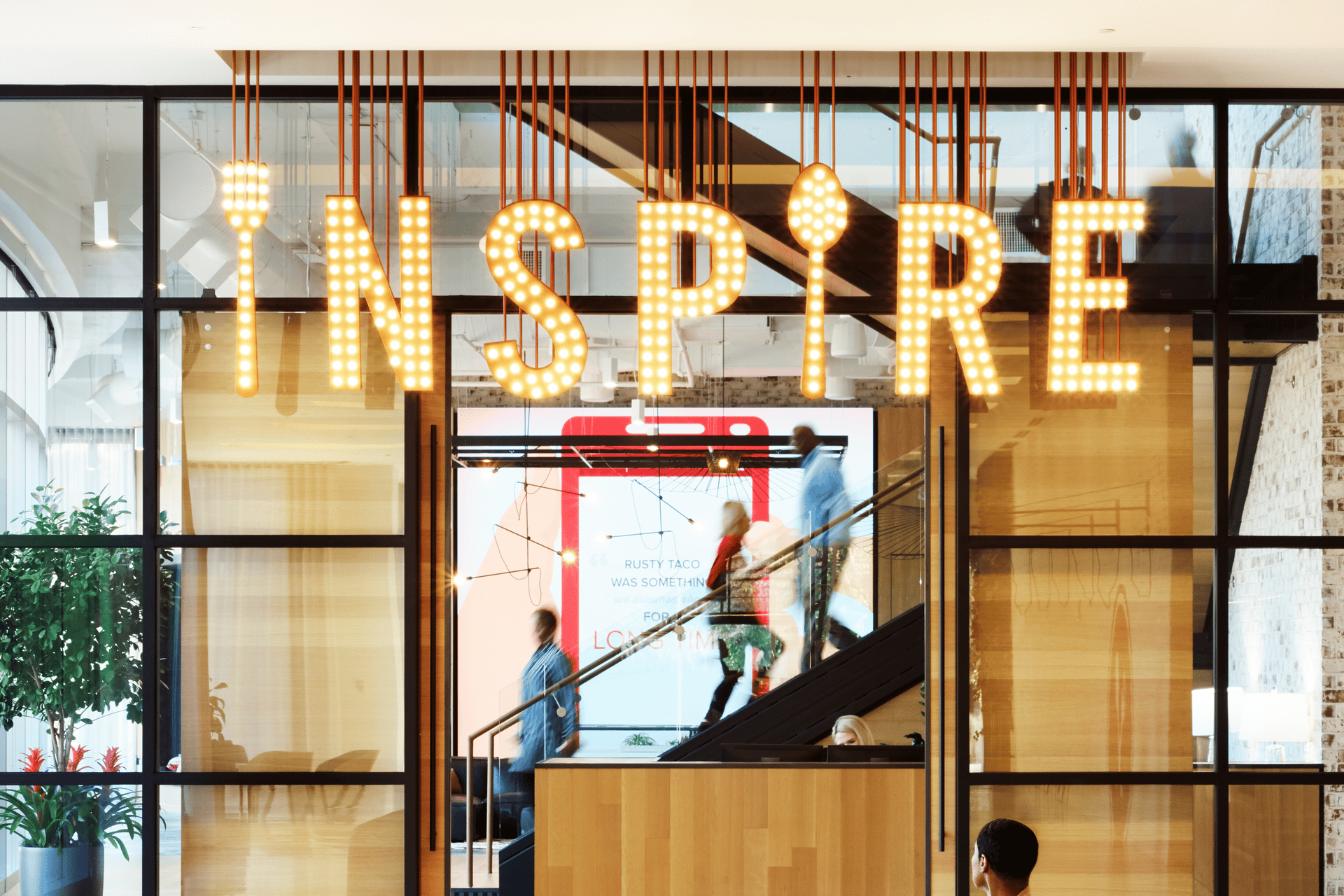
Inspire Brands CORPORATE BRANDING
Gensler Atlanta and Hannan Construction looked to Moss to provide suggestions and insight on materials, execution methods and what would ultimately work within their budget and design aesthetic for Inspire Brands’ Global Support Center in Sandy Springs, Georgia. Inspire Brands is the fourth-largest restaurant company in the U.S. and the parent of Arby’s, Buffalo Wild Wings, SONIC, Rusty Taco and Jimmy John’s.
The Center features test kitchens, fun and collaborative-spirited huddle spaces, engaging feature walls, and an Executive Board Room that steals the show with custom resin-cast door handles and a hanging sculpture spanning two floors crafted with forks and spoons.
Gensler’s design for the hanging sculpture mimicked the Inspire Brands logo of a crossed fork and spoon. The way to achieve the exemplification of the criss/cross positioning was by mounting each of the forks and spoons separately and at prescribed distances and angles.
After a series of samples and prototypes, we employed a process using a jewelry welder in order to create the tiny welds needed for the limited space available on the backs of the utensils. We also created a jig so that all the forks and spoons were positioned at correct angles. The sculpture’s hardware solution necessitated a combination of mechanical integrity to maintain tightness and an aesthetic that would be minimally intrusive for the Executive sculpture.
Another challenge was the critical desire to match the interior’s existing brick, which featured a white-wash application baked into them. The design called for the graphics to look like the actual brick color to create the graphic. The designers were emphatic that this application look as natural to real brick as possible.
Through much research, we discovered a paint product made from pulverized stone that maintains the same look and texture of stone. We experimented heavily with dilution consistencies and were able to develop a technique of painting the graphics onto treated brick surfaces on site to achieve the desired realism.
In one more example of precision and collaboration, Moss executed a wall crafted of leather hides. The raw hides delivered to Moss had jagged cuts around the perimeter and required a custom rivet-attachment method. Moss sewers hand-cut the perimeters of the hides while maintaining their natural shape. Holes for the rivets were pre-punched and our install team met with the designer onsite to work on the exact placement for the leather panels as the piece-fitting couldn’t be determined beforehand.
- Environmental Branding
- Corporate Art Solutions
- Specialty Signage Solutions
- Dimensional Letter Solutions
- On-site painting/distressing
- Living wall